Choosing The Right Gasket Material For Threaded Flanges
Choosing an appropriate gasket material for threaded flanges is critical to producing a tight and leakproof fit. Seals or gaskets protect joints, prevent leakage, and offer essential structural integrity to the cylinders.
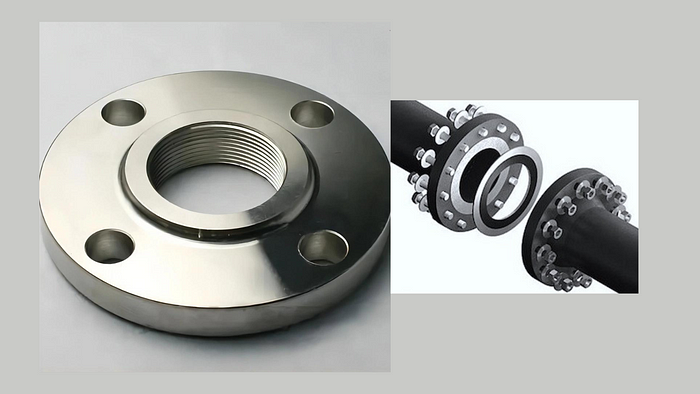
In this blog, we will consider factors that one needs to look for when selecting gasket material, including temperature exposure, pressure ratings, and application chemistry.
This guide is a roadmap for those associated with oil and gas, chemical, or manufacturing industries, providing complete knowledge.
Understanding Threaded Flanges
Threaded flanges are very necessary for joining pipes in many areas of the industry. They have a thread form of the pipe and follow the same thread standard; hence, they fit well on the pipe.
These flanges are easy to fit and dismantle and, hence, find common use where the pressure is low and the size of the pipes is also small. These are mostly used in the plumbing systems, oil and gas industry, and chemical industries using their convenience and dependable service.
This knowledge enables one to select the proper gasket material required for the design of a safe and efficient piping system.
Types of Gasket Materials
Some of the common gasket materials include the following types with certain characteristics. The main categories are nonmetallic, metallics, and semi-metallics.
Non-Metallic Gaskets
- Rubber Gaskets
- Nitrile: Good for oil and fuel resistance.
- EPDM: Excellent for water and steam applications.
- Neoprene: Suitable for weather and ozone resistance.
2. PTFE (Teflon) Gaskets
- Known for excellent chemical resistance and low friction.
3. Graphite Gaskets
- High-temperature resistance and good chemical compatibility.
4. Compressed Non-Asbestos Fiber (CNAF) Gaskets
- Versatile and used in various applications due to good chemical and temperature resistance.
Metallic Gaskets
- Ring-Type Joint (RTJ) Gaskets
Used in high-pressure and high-temperature applications.
2. Spiral Wound Gaskets
Combine metal and filler material for excellent sealing capabilities.
Semi-Metallic Gaskets
- Combination Gaskets
Made from both metallic and non-metallic materials, offering the best of both worlds.
Factors to Consider When Choosing Gasket Material
The choice of gasket material takes into account parameters such as temperature, corrosive action, pressure, and environmental factors.
Temperature Resistance
- Operating Temperatures
There is a need to check the gasket material to ensure it withstands the maximum and minimum temperatures of the given system.
2. Thermal Cycling
Focus on materials that do not degrade in response to the rapid changes in temperature.
Chemical Compatibility
- Fluid and Gas Types
Select gasket material with an adequate chemical compatibility level with the fluids or gases in your system.
2. Corrosion Resistance
Choose some products with high corrosion resistance for better durability in service.
Pressure Handling
- Operating Pressure Range
Make sure that the material used in manufacturing the gasket can withhold the pressure in your system.
2. Pressure Fluctuations
Select components that can withstand fluctuation and stress in pressure.
Environmental Considerations
- Exposure to Elements
When going for gasket material, ensure you have one that can handle weather, UV, and ozone.
2. Regulatory Compliance
Ensure the material complies with environmental regulations and industry standards.
Matching Gasket Material to Threaded Flange Applications
Several sectors demand high-quality flange gasket materials to meet the standards of their respective industries. Here are some recommendations based on common applications:
Oil and Gas Industry
- Recommended Materials: PTFE, graphite, spiral wound gaskets.
- Challenges: High temperatures and pressures, chemical exposure.
Chemical Processing Plants
- Recommended Materials: PTFE, graphite, CNAF.
- Challenges: Chemical resistance is crucial to prevent reactions.
Water and Wastewater Systems
- Recommended Materials: EPDM, neoprene, CNAF.
- Challenges: Dealing with water and steam, weather resistance.
Food and Beverage Industry
- Recommended Materials: PTFE, EPDM.
- Challenges: Hygiene and safety are paramount, so materials must be FDA-approved and easy to clean.
Installation and Maintenance Tips
Proper installation and maintenance of gaskets are essential to ensure long-lasting performance.
Installation Techniques
- Flange Surface Preparation
Clean and smooth flange surfaces ensure a good seal.
2. Correct Torque Application
Use the correct torque to avoid over-tightening or under-tightening.
Regular Inspection and Replacement
- Signs of Wear and Failure
Look for cracks, tears, and other signs of wear.
2. Preventive Maintenance
Regularly inspect and replace gaskets as part of your maintenance routine.
Conclusion
Selecting the appropriate flange gasket material for threaded flanges is critical in industries to ensure safety and optimum performance. Some factors to note include temperature, pressure, and the compatibility of the materials to arrive at the best gasket.
Ensure you adhere to the proper installation procedures and practice the right care measures for your gaskets to serve you long-lasting, durable gaskets.
A correct gasket will eliminate cases of leakage, reduce time wastage, and increase efficiency. If knowing which type of material to use is unclear, consult with professionals or manufacturers.